Smart Manufacturing: Empowering Operational Resilience Through Emerging Technologies
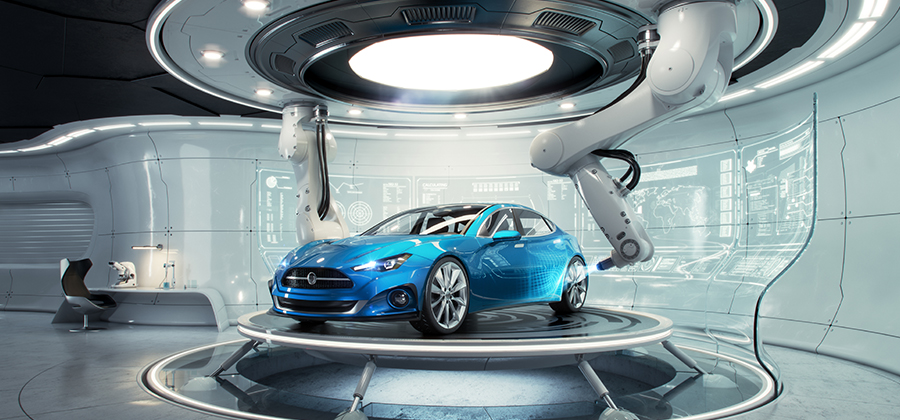
Amid the widespread disruption of the 2020s, organizations around the world are turning their attention to operational resilience, defined as “a business's ability to respond to and overcome adverse circumstances during operation that might cause financial loss or disrupt business services.”
For many businesses, a key component of operational resilience is better managing their supply chains, which have been hit hard by the pandemic, inflation, product shortages, and more. One emerging method of doing so is smart manufacturing, meaning “bringing the elements of smart technology—sensing inputs, computing power, always-on connectivity, artificial intelligence (AI), and advanced data analytics—to the traditional production process.”
As part of Citi Ventures’ ongoing series on investment opportunities in Science, Technology, Engineering, and Math (STEM)—drawing on research we conducted last year in partnership with the New York Academy of Sciences (NYAS)—we now look at smart manufacturing's roots, growth, and potential future as a source of operational resilience for firms around the world.
How We Got Here: Globalization and Supply Chain Fragility
Per our research, in the 1970s manufacturing accounted for roughly 20% of total employment in the United States. By 2020, it had fallen to 9%.
What happened? In short, the economy globalized. Starting in the 1970s, large manufacturers such as General Electric began relocating their manufacturing facilities from the U.S. to less developed nations like Mexico in order to take advantage of lower costs and/or increased productivity—a phenomenon commonly known as offshoring. That process accelerated in the 1980s and 1990s as China’s economy opened and policies like the North American Free Trade Agreement (NAFTA) encouraged free trade and open markets across the globe.
Offshoring has produced many benefits: it lowered costs and decreased time to market for many products, allowed firms to reduce labor and other expenses, and spurred economic growth in previously underdeveloped regions. However, it has also disrupted parts of the American economy and job market—particularly in the Upper Midwest, a former manufacturing hub now known as the “Rust Belt”—and contributed to the development of far-flung supply chains and “just-in-time” production concepts that have proven quite fragile in the face of recent disruptions. In 2021 alone, global supply chain pressures led leading firms across a range of industries to report an average revenue loss of $182 million each.
Smart Manufacturing and Supply Chain Resilience
Smart manufacturing may be able to help mitigate supply chain fragility and ease these pressures in a variety of ways. By applying emerging technologies such as blockchain, 3D printing, and AI to traditional manufacturing processes, smart manufacturing bolsters efficiency and innovation in manufacturing while enabling companies to pivot production quickly based on changing market needs.
In a smart factory, Internet of Things (IoT) sensors can feed real-time data into analytics systems, which can adjust machinery remotely to minimize defects, improve yield, and reduce downtime and waste. Digital simulations can also lessen the time and expense involved in creating new products and processes, while 3D printing technology can enable faster iteration and greater flexibility on factory floors.
Smart manufacturing is already demonstrating its vast potential for growth, impact, and resilience. In the early days of the pandemic, for example, the U.S. federal government partnered with the “additive manufacturing” (aka 3D printing) community to address domestic medical equipment shortages, printing and distributing more than 280,000 units of personal protective equipment (PPE) across the country in less than two months.
Smart manufacturing can also help bolster supply chain resilience by boosting onshoring or ally-shoring in key industries—that is, moving production from overseas to within a nation’s borders, or to other nations that are deemed reliable friends.
For example, one of the major contributors to current supply chain breakdowns is a global shortage of semiconductors, key components of all digital technology. The U.S. dominates semiconductor research and development (R&D) but lacks the most advanced chip factories, which largely are located in Taiwan—making the U.S. chip supply potentially vulnerable if ongoing tensions between China and Taiwan ramp up.
In response, Congress and the Biden administration are working on legislation that would authorize more than $50 billion in new spending to incentivize more semiconductor manufacturing in the U.S. A recent article from SEMI, the global industry association for electronics manufacturing and design, makes the case that investing in domestic smart manufacturing—including the STEM talent pipeline—could help alleviate future shortages while maintaining the global competitiveness of the U.S. semiconductor industry.
Manufacturing New Opportunities
But smart manufacturing does not simply offer a new way to embed resilience into global supply chains. It also presents a significant opportunity to revitalize the manufacturing industry in the U.S. and create a host of new jobs in the Future of Work.
Manufacturing remains crucial to the American economy, accounting per our research for 10.8% of total U.S. GDP, 35% of productivity growth, 60% of total exports, and 70% of private-sector R&D spending in 2020. With consumption in emerging markets expected to hit $30 trillion by 2025, a report by McKinsey Global Institute estimates that the U.S. could boost manufacturing GDP by $530 billion a year and create an additional 2.4 million jobs on top of current trends.
However, in the digital age, manufacturing is no longer seen as an enticing career path. According to Fabricators and Manufacturers Association research, 61% of U.S. teenagers said they did not see opportunities for career development or advancement in the manufacturing sector and would prefer to pursue a “professional” career instead. By investing in smart manufacturing technology, firms could help (accurately) rebrand the manufacturing sector as a hub of innovation, staffed by highly skilled workers across engineering, IT, design, and many other fields.
Smart manufacturing has the potential to be particularly game-changing for smaller manufacturers, which supply parts and products to larger firms and make up the backbone of the U.S. supply chain. Per our research, there currently is a 40% productivity gap between small and large manufacturing firms, primarily because smaller firms have fewer resources and capabilities than larger firms. Adopting new smart manufacturing technologies and procedures and investing in related R&D could help close this gap.
Smart manufacturing could also help rejuvenate the Rust Belt. Upper Midwest cities such as Cleveland, Ohio have much to offer: low-cost labor, convenient connections to major thoroughfares, existing industrial infrastructure, needed technical expertise, and local access to the broader manufacturing ecosystem. Combining these strengths with the improved productivity and efficiency associated with smart manufacturing could transform older industrial hotspots into newly competitive regional manufacturing hubs—springboards for various resilient and growth-promoting innovations.
Working Together for the Future of Manufacturing
Disruption at global scale deeply impacts both public life and private industry; thus, the most effective responses to it often merge the two. Investors, industry leaders, and policymakers all can play key roles in fostering resilience—both by jointly developing, managing, and funding smart manufacturing initiatives and by prioritizing the STEM education pipeline to equip students and workers with smart manufacturing-enabled skills.
The Manufacturing USA Institutes offer a template for how the public and private sectors can work together to develop the smart manufacturing ecosystem. Supported by state governments, federal agencies, and private industry alike, this national network of 16 manufacturing institutes with unique technological concentrations such as biofabrication and advanced fabrics trains workers, tests applications, and convenes stakeholders to collaborate on R&D. That helps reduce the financial risks associated with deploying new technologies—a major concern for smaller manufacturers—fostering further innovation and faster development of advanced manufacturing within the U.S.
For banks and other financial institutions, opportunities abound to finance manufacturers’ transitions to a smarter, more connected future. Citi Ventures and the Citi Impact Fund have also invested in smart manufacturing startups Factory_OS and ICON, helping these innovative young companies reach the scale they need to support operational resilience in the 21st century. Stay tuned for more!